The world of metalworking is undergoing major changes. Complex machining processes are unimaginable without the utilization of face milling operations. Face milling processes facilitate the preparation of datum surfaces by producing planes and flats, and enable improving precision and surface quality parameters. Moreover, the production of many rotating parts is incomplete without face milling. Face milling is the very operation that cannot be undermined.
In face milling, the axis of a cutter is normal to the machined surface. A large majority of face mills or surface milling cutters are common indexable tools in shell mill configuration. They feature various tool cutting edge angles (entering angles) such as 45°, 60°, 65°, 75°, 90°. Face mills intended specifically for productive rough machining by use of high feed milling (HFM) methods have a significantly smaller cutting-edge angle, typically 10°-17°. In some cases, shell mills that mount round inserts enable extremely strong cutting edges. The cutting-edge angle has an impact on the decomposition of the cutting force, which acts on the plane of the cutter axis, on radial and axial components referred to as radial, and axial cutting forces. With all else being equal, this angle defines the maximum depth of cut. The cutting-edge angle largely determines the application field of a face mill making 45° face mills most versatile. Such mills have an important advantage that stipulates a first-choice selection of 45° cutters in face milling, specifically when machining open plane surfaces. These cutters assure a good balance of radial and axial cutting forces, a high-quality machined surface, and favorable cutting conditions when a tool enters or exits the material being machined. The most common face mill types are 45° cutters.
However, 45° face mills have certain disadvantages with an emphasis on forming rectangular profiles. Although machining square shoulders characterizes end milling applications, there is a need for rectangular profiles as well. All plane surfaces of a machined part are bound by shoulders. Applying 45° face mills even when cutting near to shoulders may entail difficulties. Face mills with 90° cutting edge angles are regularly in demand for rectangular profiles. In addition, 90° tools assure low axial forces providing good reason for machining parts with thin-walled structures or cutting under poor clamping conditions. Beyond that, inserts for 90° face mills provide a higher depth of cut when compared to the same-size inserts, intended for 90° endmills.
The correct and sensible method to design 90° face mills utilizes the same inserts that are intended for 90° endmills. This concept provides high insert versatility and remains prevalent. To ensure a good surface finish, the inserts of large diameter multitoothed indexable face mills should be designed with a wiper flat that is significantly larger compared to an endmill, which is characterized by fewer teeth. Tool manufacturers maintain various principles in their developments which focus on productivity solutions, shoulder profile accuracy, and the efficient utilization of tungsten carbide being the main material of indexable inserts. The ideal design provides excellent solutions and complies with competitive machining requirements.
NEODO S90° is a family of 90° face mills that mount 8 mm double-sided square carbide inserts (Fig. 1). This family of inserts is intended for rough and semi-finish machining of steel and cast iron. The double-sided insert concept shows a durable insert structure and facilitates 8 indexable cutting edges. The insert may appear simple, but when looking closely, the insert side surface features a complex shape that provides a wide wiper flat on every cutting edge. The face mills have a positive radial and negative rake angle and ensure an exact 90° profile when milling with depths of cut up to 5 mm. The NEODO S90° cutters enable face and shoulder milling while providing an additional option for machining close to shoulders where workpieces or work holding fixtures entail constraints.
In small tool diameter ranges between 32-63 mm, ISCAR introduces a family of the HELIDO Trigon Line (Fig. 2). This family of tools is characterized by high-tooth density face mills with double-sided trigon-shaped inserts for true 90° profiles at a depth of cut up to 4 mm for ultra-high productivity. The insert's trigon shape provides 6 indexable cutting edges and forms positive tool rakes in both radial and axial directions. Combined with a wide wiper flat, the insert's design contributes to an improved surface finish and easily performs ramp-down milling.
LOQIQ-8-TANG face mills (Fig. 3) mount tangentially clamped inserts with 8 cutting edges and provide a cost-beneficial solution for rough machining planed surfaces near square shoulders. The tangential insert mounting concept combined with a dovetail clamping principle and a durable insert structure results in a strong and rigid tool design to withstand heavy loads in roughing applications.
ISCAR has upgraded the HELIQUAD family of 90° mills with traditionally designed single-sided square inserts. Specifically, the new inserts are intended for machining titanium and heat-resistant superalloys (HTSA), especially when milling near-to-shoulder faces.
In milling applications that require small tool diameters, MULTI-MASTER solid carbide exchangeable face milling heads in diameters of 12-25 mm can provide effective results (Fig. 4). Due to the multi-tooth design, the heads guarantee productive cutting at high feed speeds. An important advantage of this unique face milling head is its high precision attributes, which are comparable with those of solid carbide tools. Such precision levels result in increased machining accuracy and excellent surface finish.
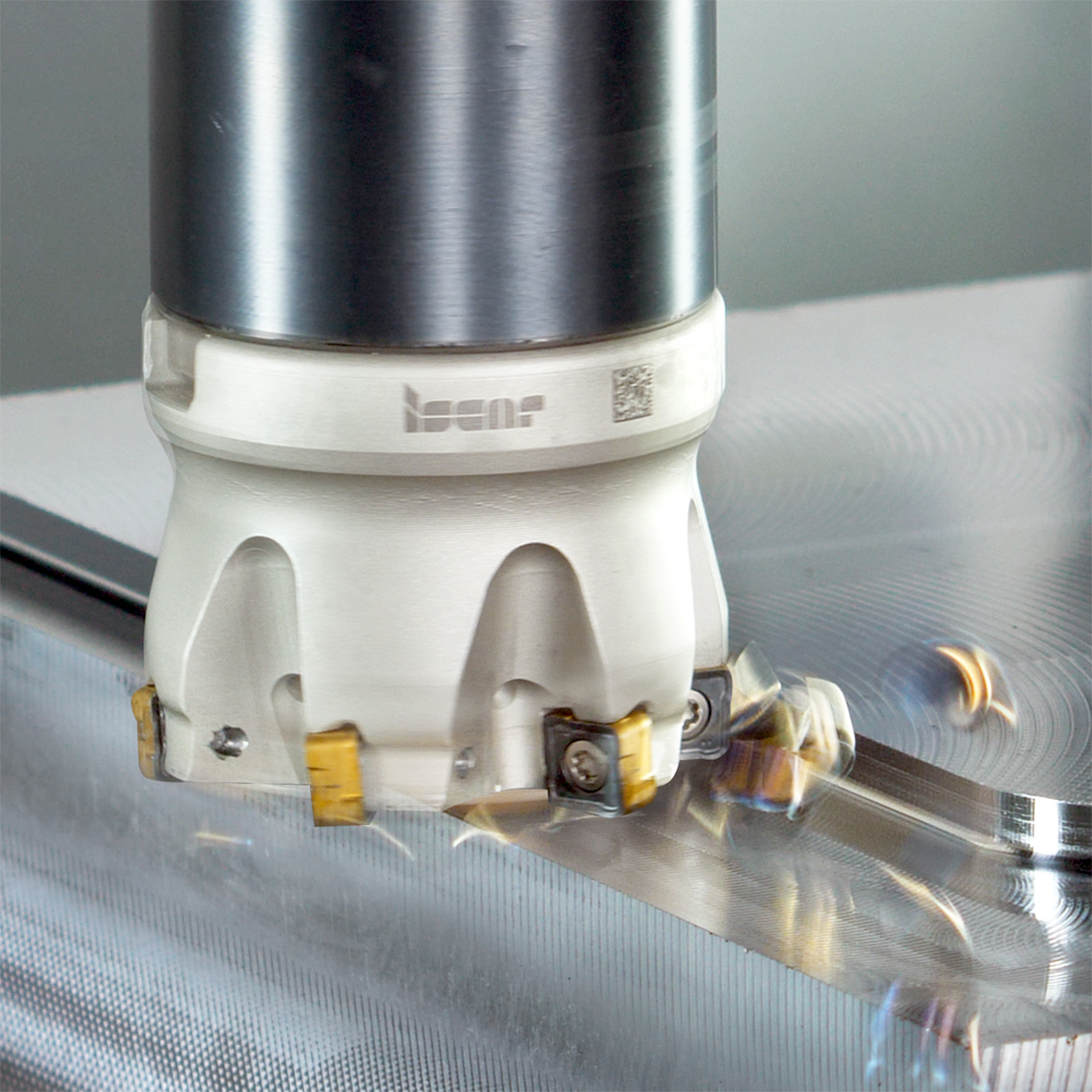
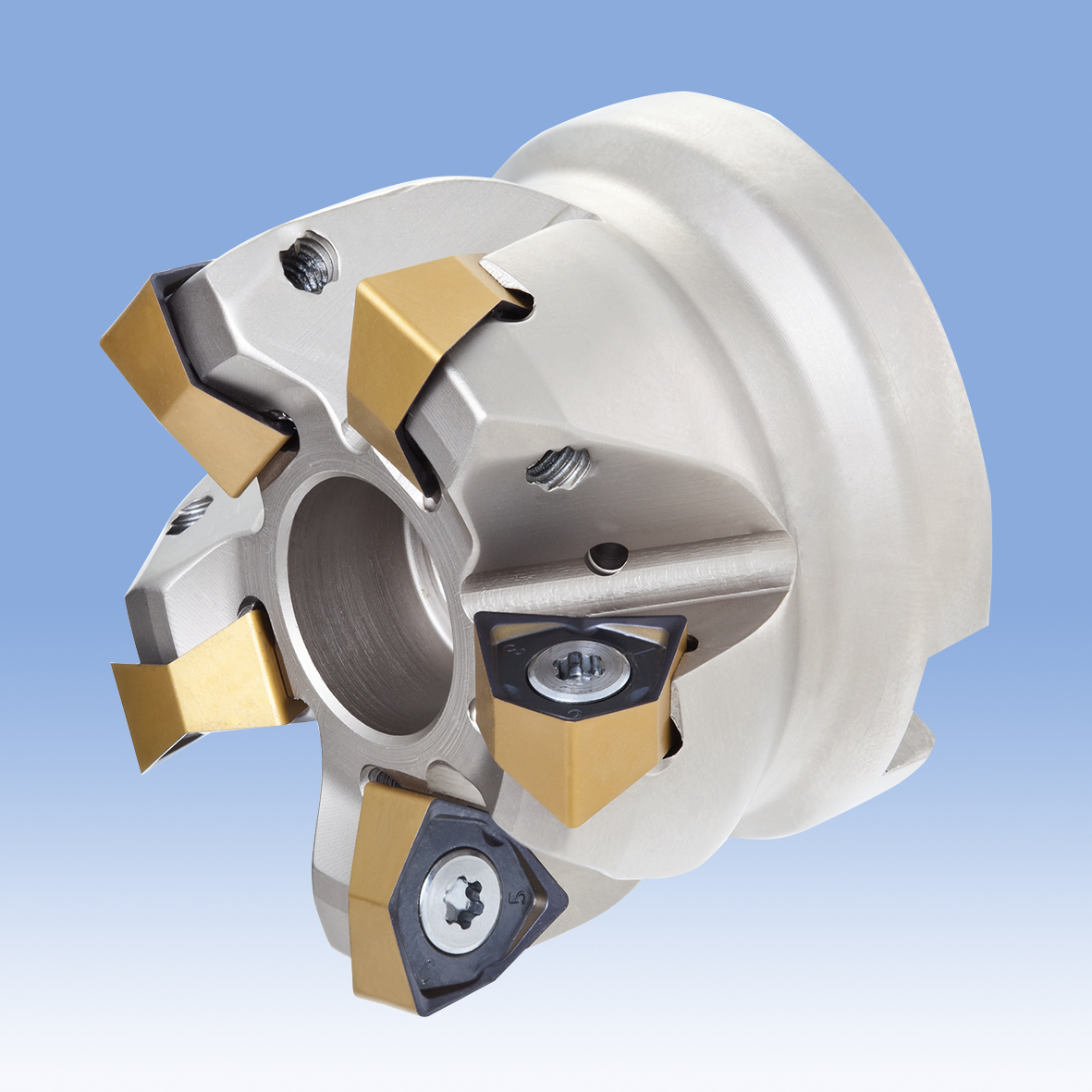
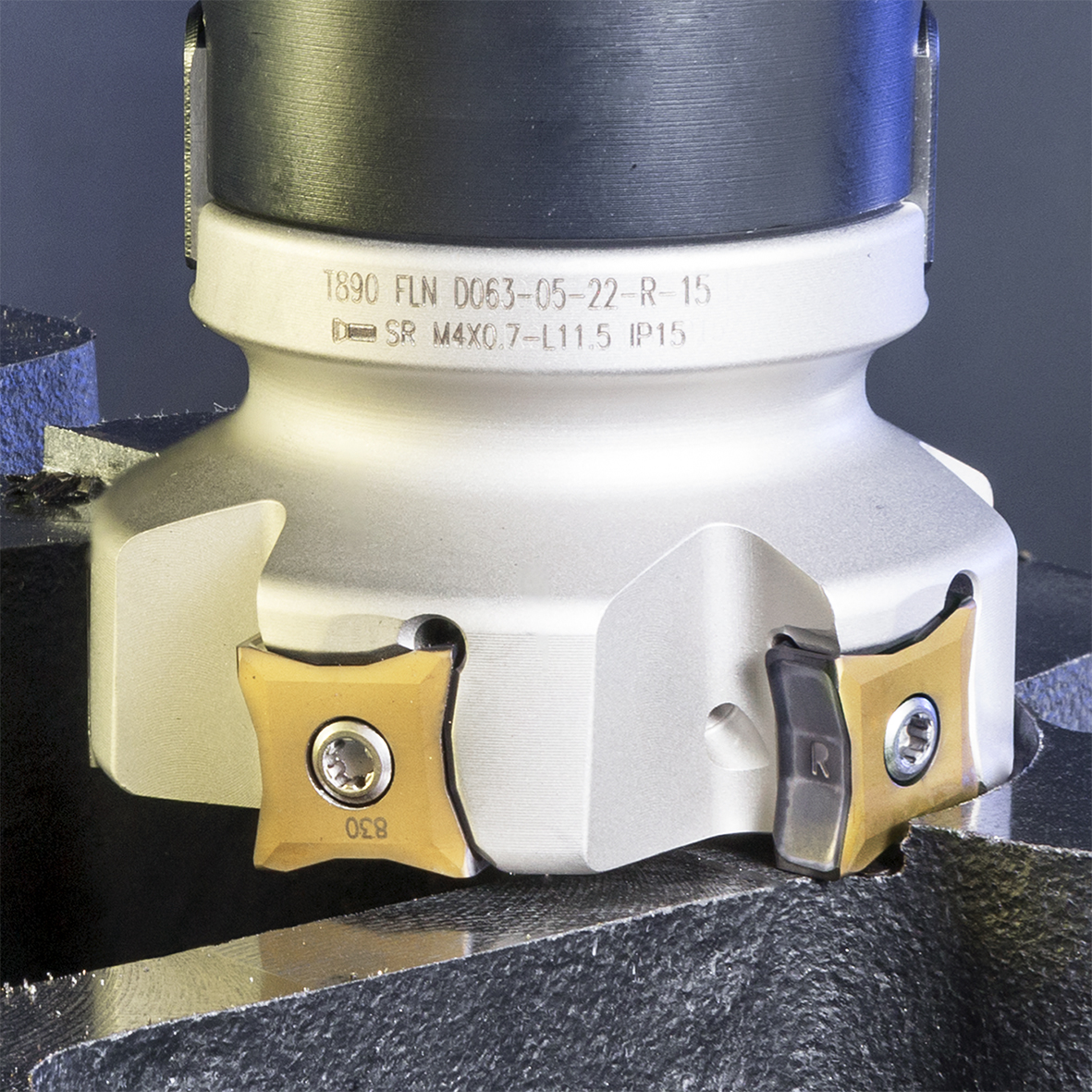
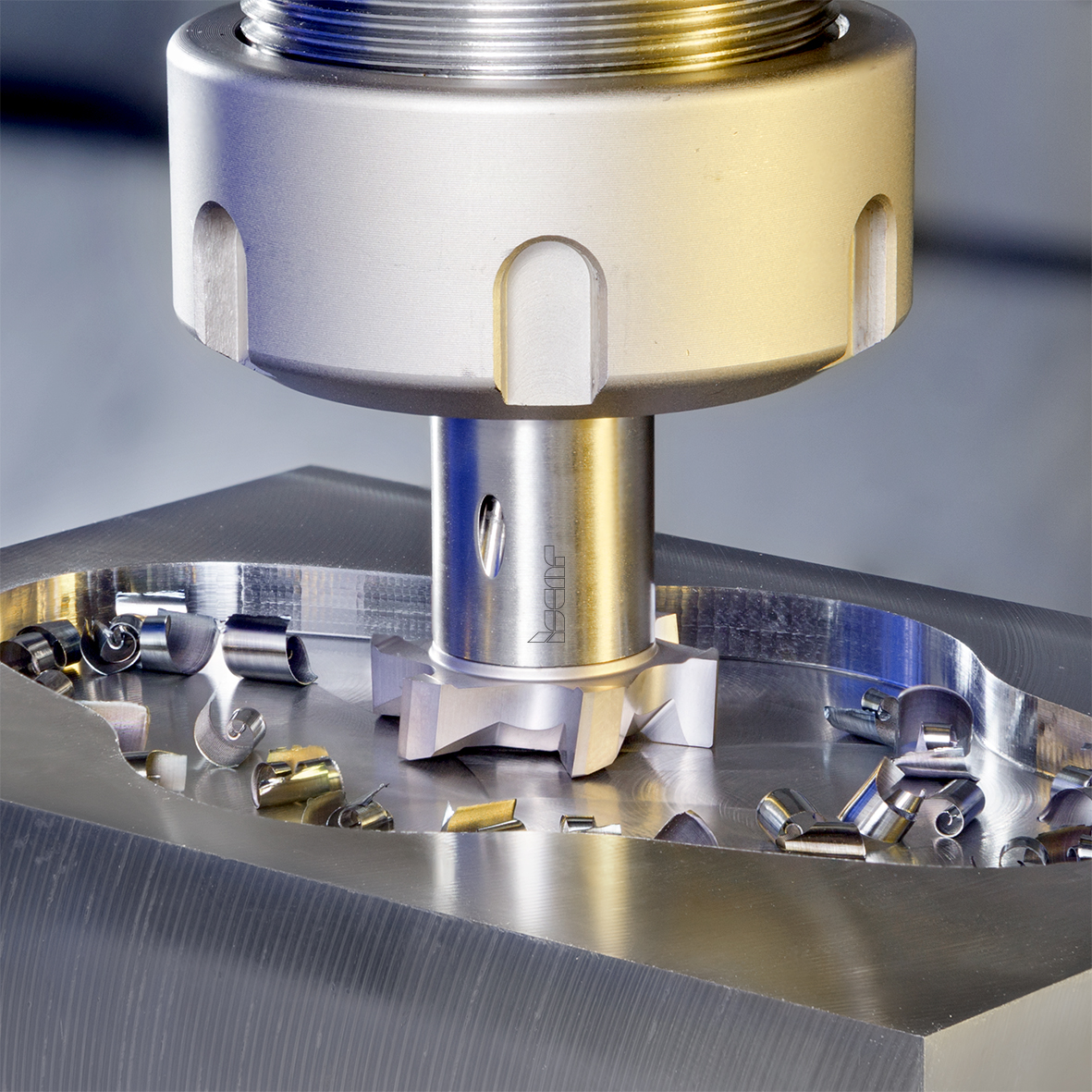